The Top Three Skills Manufacturing Executives Seek in New Hires
Posted by Michelle Ecker on June 4, 2020
In a recent study of global talent deficit, Korn Ferry and Man Bites Dog consulting groups collaborated with Oxford Analytica to produce an economic model that would outline future labor supply and demand at impending milestones, particularly highlighting the years 2025 and 2030 in their findings. What their research uncovered is that three distinct economic markets are significantly threatened by a growing shortage of trained workers- financial and business services, media and telecommunications, and manufacturing.
These economic models found that without proactive action to disrupt this trend, the mounting shortage will create 85.2 million unfilled jobs and 8.5 trillion dollars in bygone revenue within these three at-risk industries throughout the coming ten years.
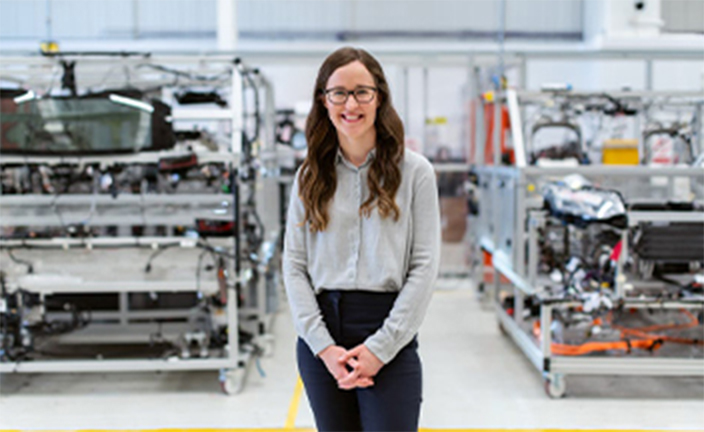
Inside the manufacturing skills gap
Manufacturing talent shortages have been a point of concern voiced by industry leaders since 2017, but are now nearing a distressing historical peak unseen within this sector in nearly two decades. And while the imminent widening of this skills gap is no doubt alarming, lost in today’s conversation regarding projections is the fact that leaders are not simply sharing concerns for the future of the workforce - they are struggling today. Latest surveys by Deloitte and The Manufacturing Institute reveal that 89% of manufacturing industry executives say they are currently facing a talent crisis within their industry.
Leaders in education and upskilling suggest this missing talent is the result of technology’s impact on the day to day role of the manufacturing worker. In essence, the manufacturing jobs of today require digital skills more than ever before, and the current workforce may not all be sufficiently trained to operate and work alongside this new technology. In an effort to combat this disjunction, manufacturing leaders need to acknowledge these skills gaps and take a lead in upskilling the workforce of the present and future. By training today’s workers to properly keep up with a shifting, technology-focused skill set requirement, manufacturing leaders can take the first steps to prevent a mounting workforce crisis in their industry.
For many leaders, this strategy can start with pinpointing things like the antiquated jobs and skills no longer relevant to today’s workflow, the specific skills missing from a productive internal workforce, and the educational options available to train workers in transitioning from one to another.
To give context to this imminent shift in the industry at large, Deloitte insights predict forty-seven percent (2) of the manufacturing roles leaders are accustomed to filling today will likely be gone in the next 10 years. This is not because opportunity within the industry is projected to shrink, in fact quite the opposite - overall headcount necessary to perform day to day operations is expected to increase. (3) With 47% of today’s jobs and corresponding skills disappearing but sheer workforce headcount requirements poised to grow, clearly we are facing a crossroads in which talent sourcing and workforce upskilling will become an integral factor. In preempting this shift, it would seem crucial for industry leaders to pointedly identify which current jobs are growingly obsolete, compared to which jobs are being created alongside new technological innovations, then plan a way to help shift their workforce from one to the other with provided training solutions and formal education.
“The world can’t afford to have tens of millions of unfilled jobs and trillions of dollars in unrealized revenue,” said Alan Guarino, vice chairman, Korn Ferry CEO and Board Services. “Companies must work to mitigate this potential talent crisis now to protect their future. If nothing is done, this shortage will debilitate the growth of key global markets and sectors.”
What manufacturing jobs are being created?
Manufacturing executives were asked to share which skill sets they feel they will have the largest growing need to fill within the coming three years, specifically due to the introduction of new technology within the manufacturing workplace. Largely, they responded (4) by sharing a need for employees trained in:
- Technology/computer skills
- Working with tools and technology
- Critical thinking skills
Essentially, the future of the manufacturing workplace largely points to one in which more robots and technology will be embedded across workplace functions, and employees will need to be trained to operate, maintain, and work alongside said technology as part of their new daily routines. And as many technological advances are occurring at a rapid pace, not all workers within the industry have the new skills they need to succeed. With the impending retirement of boomers from the manufacturing sector, a new generation of workers must be trained in these skills in order to sufficiently replace those leaving retirees.
Within the manufacturing industry, if we’re now seeing a clear disconnect between the type of work employers need employees to perform, and a workforce currently struggling to fill these roles because of a lack of training, a meeting in the middle clearly lies at the solution to this talent crisis, with more accessible, practical education lying at the heart of what’s missing from the conversation.
Providing education to manufacturing workers
By identifying key missing skills such as the three listed above, then providing employees and the next generation of workers with educational options that will sufficiently train them in said skills, we can proactively close the gap between what’s missing and what’s necessary for the sustainable growth of the manufacturing industry in the future.
Leaders in education and upskilling are already working to offer training solutions to help manufacturing employers solve for this need. As one of these educational leaders, Penn Foster offers online skills training and educational programs along with academic support and student services to the manufacturing workers of today, in an effort to train workers in the skills such as those listed above. From condensed pathway programs designed to meet specific, tailored employer needs, to multi-year degree programs and career diplomas, Penn Foster’s skills-based portfolio of online education and remote training solutions were designed to help provide upward career mobility to today’s workers while delivering productivity and efficiency outcomes within any manufacturing organization. For more information on how Penn Foster’s programs can meet your unique training needs, contact a Penn Foster training expert today.
Endnotes:
2,3,4: Deloitte Insights, “The jobs are here, but where are the people?” November, 2018. View in article.